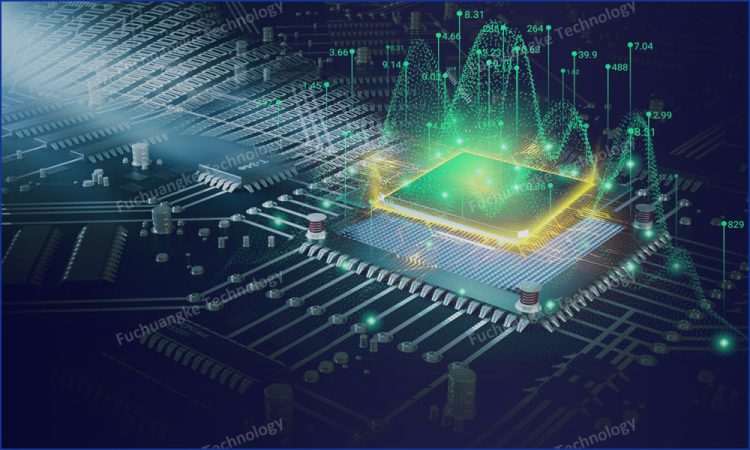
As technology continues to advance, printed circuit boards (PCBs) have become an integral part of many electronic devices. These small, complex components are responsible for connecting and controlling the various parts of electronic devices, and their reliability and performance are crucial for ensuring the overall functionality of the device. In this article, we will explore why quality control is so important in PCB manufacturing and how it can benefit customers who rely on these components.
The Role of Quality Control in PCB Manufacturing
PCB manufacturing involves several stages, including design, fabrication, and assembly. Each stage is important for creating a functional, reliable PCB, and quality control is critical at every step of the process.
During the design stage, engineers work to create a PCB that meets the specifications of the customer’s electronic device. Quality control at this stage involves reviewing the design for potential issues and making necessary adjustments to ensure that the final product will meet the customer’s requirements.
In the fabrication stage, the design is translated into an actual PCB. Quality control at this stage involves checking the materials used, ensuring that the board meets the required specifications, and checking for defects or issues that may affect its performance.
Finally, during the assembly stage, components are added to the board to create a functional PCB. Quality control at this stage involves ensuring that the components are properly installed and that the final product functions as expected.
Benefits of Working with a Supplier that Prioritizes Quality Control
Working with a supplier that prioritizes quality control can provide several benefits for customers. First and foremost, high-quality PCBs can improve the performance, reliability, and longevity of electronic devices. By catching defects early and ensuring that the PCB prototype meets the necessary specifications, a supplier of printed circuit boards can help customers avoid costly mistakes and delays.
In addition, a supplier’s commitment to quality can increase customer confidence and satisfaction. By working with a supplier that has robust quality control processes in place, customers can feel assured that they are getting a reliable, high-quality product that will meet their needs.
Quality Control Measures Used in PCB Manufacturing
There are several quality control measures that are commonly used in PCB manufacturing. These include visual inspections, automated testing, and X-ray inspections.
Visual inspections involve inspecting the PCB with the naked eye to check for any visible defects or issues. Automated testing involves using specialized equipment to test the functionality of the board and ensure that it meets the required specifications. X-ray inspections use X-ray technology to look inside the PCB and check for defects that may not be visible to the naked eye.
Conclusion
In summary, quality control is critical in PCB manufacturing to ensure that the final product is functional, reliable, and meets the customer’s requirements. Working with a supplier that prioritizes quality control can provide several benefits for customers, including improved performance, reliability, and customer satisfaction. By understanding the importance of quality control in PCB manufacturing, customers can make informed decisions when selecting a supplier and ensure the best possible results for their electronic devices.