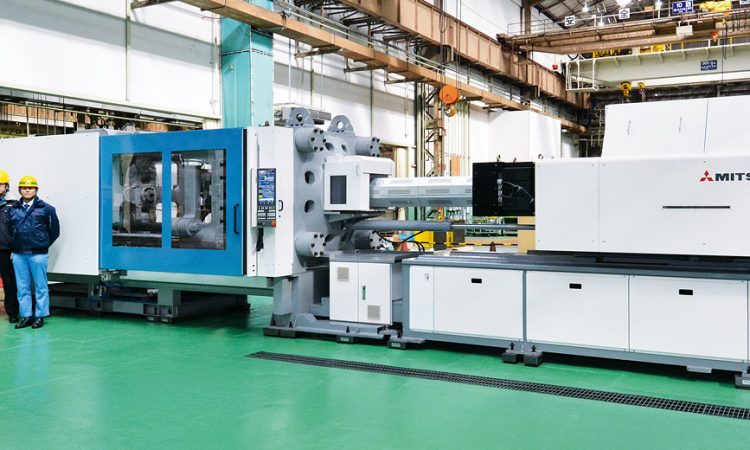
Injection molding is a widely used manufacturing process that revolutionized the production of plastic parts and components. As technology has evolved, heavy injection molding has emerged as a critical technique for large-scale production of bulky and complex plastic parts.
In this article, we will delve into the world of heavy injection molding, exploring its benefits, applications, and the challenges it overcomes.
What is Heavy Injection Molding?
Heavy injection molding is an advanced form of traditional injection molding, specifically designed to manufacture large and heavy plastic parts. This process involves injecting molten plastic material into a mold cavity, which is shaped like the desired product, and then allowing it to cool and solidify to create the final component.
Unlike standard injection molding, which predominantly focuses on small to medium-sized parts, heavy injection molding deals with parts that are typically measured in pounds, rather than ounces.
Benefits of Heavy Injection Molding
Enhanced Durability: Heavy injection molding allows manufacturers to produce robust and durable plastic parts, capable of withstanding significant stress, mechanical load, and environmental conditions. Industries such as automotive, aerospace, and construction benefit greatly from these sturdier components.
Cost Efficiency: Despite the higher initial setup costs, heavy injection molding often proves more cost-efficient for large-volume production runs. The ability to manufacture multiple identical parts in a single mold significantly reduces per-part costs and increases overall profitability.
Complex Geometries: The process of heavy injection molding enables the creation of intricate and complex part designs. From large automotive panels with intricate patterns to industrial containers with multiple integrated features, this method allows engineers to push the boundaries of part complexity.
Material Variety: Heavy injection molding supports a wide range of plastic materials, from common thermoplastics like polyethylene and polypropylene to more specialized engineering plastics like polycarbonate and ABS. Manufacturers can choose materials that suit specific requirements for strength, chemical resistance, and more.
Applications of Heavy Injection Molding
Automotive Industry: Heavy injection molding plays a pivotal role in the automotive sector, where it is used to manufacture various large components such as bumpers, dashboards, body panels, and interior parts. These parts require high strength, precision, and aesthetic appeal, which heavy injection molding can deliver.
Industrial Equipment: In the realm of industrial equipment and machinery, heavy injection molding is utilized to produce large-scale parts like housing enclosures, equipment panels, and covers. These parts need to withstand harsh operating conditions and provide protection for the internal machinery.
Aerospace and Defense: In the aerospace and defense sectors, heavy injection molding is employed to fabricate large components like aircraft wings, fuselage parts, and missile casings. The process ensures consistency, strength, and precision in manufacturing critical parts for these industries.
Challenges and Considerations
While heavy injection molding offers numerous advantages, it also presents certain challenges that manufacturers need to address:
Equipment Size and Capability: Heavy injection molding requires specialized machines capable of handling larger molds and injecting significant volumes of molten plastic. Such machines can be expensive and may require substantial floor space.
Material Flow and Cooling: Ensuring uniform material flow and even cooling throughout the large mold can be challenging. Improper cooling can lead to defects like warping, sink marks, and uneven wall thickness, compromising the final product’s quality.
Cycle Time: The larger size of parts in heavy injection molding increases the cycle time, affecting production efficiency. Balancing cycle time with cooling rates is essential to achieve maximum productivity.
Conclusion
Heavy injection molding has emerged as a vital technique for manufacturing large and robust plastic parts used in various industries. Its ability to create durable and complex components, along with cost efficiency for high-volume production, makes it a cornerstone of modern industrial manufacturing.
As technology continues to advance, heavy injection molding will likely play an even more significant role in shaping the future of plastic component fabrication.